Heat Treatment Technology for CNC machined parts
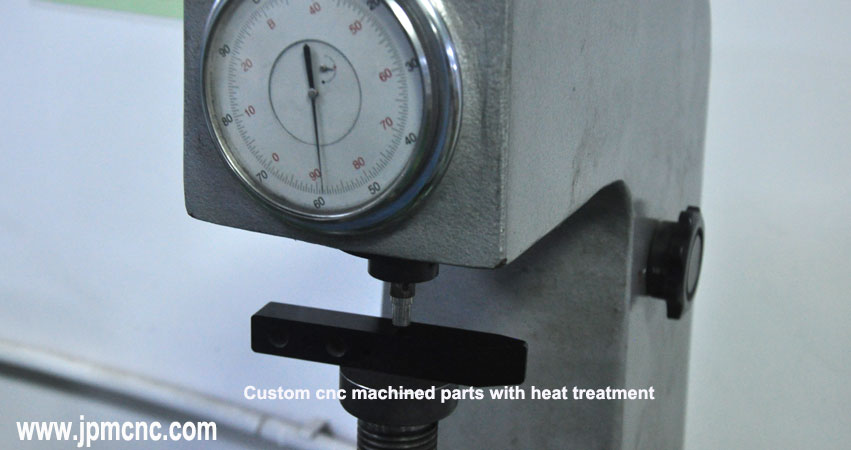
Machined components
What is heat treatment of CNC machined parts and its application?
The heat treatment of cnc machined parts generally refers to a process in which a material has a phase transition above a phase transition temperature, followed by cooling to undergo a phase change. Through this phase change and re-transformation, the internal organization of the material changes and thus the performance changes.
A large number of cnc machined parts used in machine tools, automobiles, motorcycles, trains, mining, petroleum, chemical, aerospace, aerospace, etc. Therefore we need improve its’hardness by heat treatment processes. Rejecting preliminary statistics, in machine tool manufacturing, about 60% to 70% of parts are subject to heat treatment. In automotive and tractor manufacturing. Parts requiring heat treatment are as much as 70% to 80%, while tooling and rolling bearings are 100%. Heat treatment is reachable. In short, all important parts must be properly heat treated before using them.
Heat Treatment increase hardness of material
For example, the carbonized tool steel T8 commercially available spheroidized annealed material has a hardness of only 20HRC. As a tool, it needs to be quenched and tempered at low temperature. Makes increasing the hardness to 60~63HRC, because the internal structure is before quenching. The granular pearlite can transform into tempered martensite after quenching and low temperature tempering. The heat treatment process of the same material is different, and its performance varies greatly.
Table 6-1 lists the mechanical properties of uniform steel rods of 45 steel with a diameter of F15mm after annealing, normalizing, quenching and low temperature tempering, and quenching and high temperature tempering. The reason for the difference in performance is so large. The internal organization is quite different after different heat treatments. The heating temperature of material (for example, quenching) commonly depends on the material composition. These indicate that the heat treatment process (or system) selection depends on the composition of the material. The internal organization of the material changes depending on the material heat treatment and other thermal processing processes. The change in material properties depends on the internal structural changes of the material. The material composition – processing technology – The structure of the four structures of the structure-material properties intersperse throughout the entire process of material processing.
The basic elements of heat treatment
Heating is the first step in the heat treatment. Different materials have different heating processes and heating temperatures. There are two types of heating, one is heating below the critical point A1, and no tissue change occurs at this time. However the other is heating above A1.There are three basic elements in the heat treatment process: heating, heat preservation, and cooling. These three basic factors determine the organization and properties of the material after heat treatment. We must consider of these elements before we have a heat treatment of cnc machined parts.
Common Heat Treatment Concepts
Normalizing
The cnc machined parts are heated in a suitable temperature. Above the critical point Ac3 or above for a certain period of time and then cooled in the air to obtain a heat treatment process of the pearlite-like structure. Normalizing is to cool the cnc machined parts to a suitable temperature and then cool it in the air. The effect of normalizing is similar to annealing, but the resulting structure is finer, which is often used to improve the cutting performance of materials. Sometimes used for some less demanding parts. As the final heat treatment.
Annealing
Heating the hypoeutectic steel workpiece to 30-50 degrees above Ac3. After a period of heat preservation, the furnace cool down (or buried in sand or lime) to a heat treatment process of cooling below 500 degrees in air. Annealing is to heat the CNC machined workpiece to the appropriate temperature. Spending different holding time according to the material and the workpiece size, and then slowly cooling. In order to make the internal structure of the metal reach or close to equilibrium, obtain good process performance and performance, or further quench Organization.
Solution heat treatment
Heating the alloy to a high temperature single-phase zone constant temperature. So that the excess phase is sufficiently dissolved at a rapid rate to obtain a heat treatment process of the supersaturated solid solution.
Aging
The phenomenon that the properties of a alloy change with time after being subjected to solution heat treatment or cold plastic deformation at room temperature or slightly above room temperature
Solution treatment
Fully dissolve various phases in the alloy, strengthen the solid solution and improve toughness and corrosion resistance, eliminate stress and soften, and continue processing.
Aging treatment
Heating and holding at the temperature of the strengthening phase, allowing the strengthening phase to precipitate and harden, improving strength.
Quenching
A heat treatment process in which operater can austenitize and cool the cnc machined parts at an appropriate cooling rate. This causes the workpiece to be decomposed into the solid solution in all or a certain range of the cross section. Then the unstable microstructure structure such as martensite is rapidly formed. Quenching is the rapid cooling of the workpiece after heating and holding it in a quenching medium such as water, oil or other inorganic salts or organic aqueous solutions. After quenching, the steel becomes hard but becomes brittle at the same time.
Tempering
Heating the quenched workpiece to a suitable temperature below the critical point Ac1 for a certain period of time. Followed by cooling in a satisfactory manner to obtain the desired microstructure and properties of the heat treatment process. In order to reduce the brittleness of the steel, quenching The latter steel is subject to long-term heat preservation at a suitable temperature above room temperature and below 710 ° C. And then cooled, and this process is called tempering. Annealing, normalizing, quenching and tempering are the “four fires” in the overall heat treatment. Among them, the quenching and tempering are closely relative, and often used together, they are indispensable.
Quenching and tempering
The heat treatment combined with quenching and high temperature tempering is called quenching and tempering. Quenching and tempering is widely used in a variety of important structural parts. Especially those that work under alternating loads, such as connecting rods, bolts, gears and shafts. After quenching and tempering treatment. The tempered sorbite structure is obtained, and its mechanical properties are superior to the normal-fired sorbite structure of the same hardness. Its hardness depends on the high temperature tempering temperature and related to the tempering stability of the steel and the cross-sectional dimensions of the workpiece. Generally between HB200 and 350.
What is the nitriding process?
Nitriding is using specialized equipment or a well type carburizing furnace. Applicable to all kinds of high-speed transmission precision gears, machine tool spindles (such as masts, grinding machine spindles), high-speed diesel engine crankshafts, valves, etc. It also blongs to one kind of heat treatment of cnc machined parts.
Nitriding workpiece routing: forging – annealing – roughing – quenching – finishing – stress removal – rough grinding – nitriding – fine grinding or grinding.
Since the nitrided layer is thin and brittle, it requires a higher strength of the core structure, so the tempering heat treatment is first perform the tempered sorbite, and even more to improve the mechanical properties of the core and the quality of the nitrided layer.
After nitriding, steel no longer needs to be quenched to have high surface hardness and wear resistance.
The nitriding treatment has a low temperature and little deformation
. Compared with carburizing and induction surface quenching, the deformation is much smaller. (2) Carbonitriding of steel: Carbonitriding is the simultaneous infiltration of carbon and nitrogen into the surface of steel. The process, customary carbonitriding, also called as cyanidation. At present, the application of medium temperature gas carbonitriding and low temperature gas nitrocarburizing (ie, gas soft nitriding) is widely used. The main purpose of carbon monoxide in medium temperature gas is to improve the hardness, wear resistance and fatigue strength of steel. The low temperature gas carbonitriding is mainly nitriding, and its main purpose is to improve the wear resistance and seizure resistance of steel.
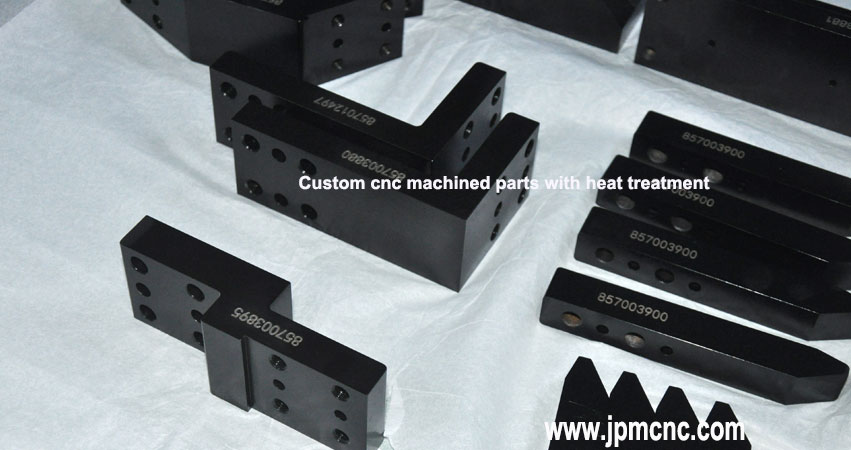
Machined parts
JINXIN is a precision machined parts vendors in China, we supply custom manufacturing service including Precision CNC milled parts and Precision Turned Components that are widely used for the industry such as Aerospace, Defense, Automotive, the automobile industry.
15+ experience:
JIngxin has over 15 years of experience high precision machined components Located in Dongguan City China. JINGXIN’s Professional team adopt reasonable manufacturing solution and workmanship to supply high-quality one-stop custom manufacturing services.
Focus :
JINGXIN focus on custom Non-standard CNC precision machined parts such as Fittings, valves, hydraulic components, electric motor parts, transmission and pump parts, sprocket wheels, wear parts on packing machines and electronic and medicinal pieces
Welcome to contact our Project Manager (Mr. Sammy: enquiry@jpmcnc.com) directly for your projects.
Https//www.jpmcnc.com
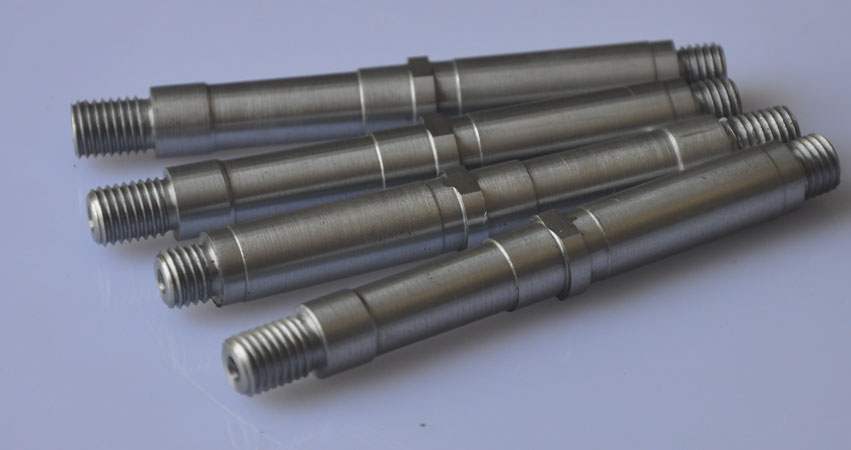
CNC machined shaft