Top 8 Deviations to CNC Precise Machining And Manufacturing
In Precise Machining and Manufacturing Process ,Machining deviation means the degree of deviation between the actual geometric parameters (geometry liner, form and position) of the part after machining and the designed geometrical parameters. The degree of coincidence between the actual geometrical parameters and the ideal geometrical parameters is called as Deviations to CNC Precise Machining And Manufacturing.
The smaller the machining deviation, the higher the degree of conformity and the higher the machining accuracy. Machining accuracy and machining deviation are two standards of quality level. Therefore, the size of the machining deviation reflects the level of machining accuracy.
The 8 Main Factors Of Impact Machining Deviations
1.CNC machines’ deviations
Spindle rotation deviation, rail deviation and drive chain deviation.
Spindle rotation deviation: The spindle rotation deviation reflects the variation of the actual rotation axis of the spindle. It is relative to its average rotation axis at each moment, which will directly affect the accuracy of the part machined. The main causes of the spindle rotation deviation are the spindle’s coaxial error, the bearing’s own error. The coaxiality deviation between the bearings and the spindle’s winding degree.
Guide Rail deviation: The guide rail is the reference for determining the relative position of each machine part on the machine tool. This is also the reference for the machine tool movement. The manufacturing deviation of the guide rail itself. However the uneven wear of the guide rail and the mounting quality are important factors causing the guide rail deviation.
Drive chain deviation: It refers to the deviation of the relative motion between the transmission elements at the end of the drive chain. It is caused by the manufacturing and assembly deviation in the various components of the drive chain and the wearer during use.
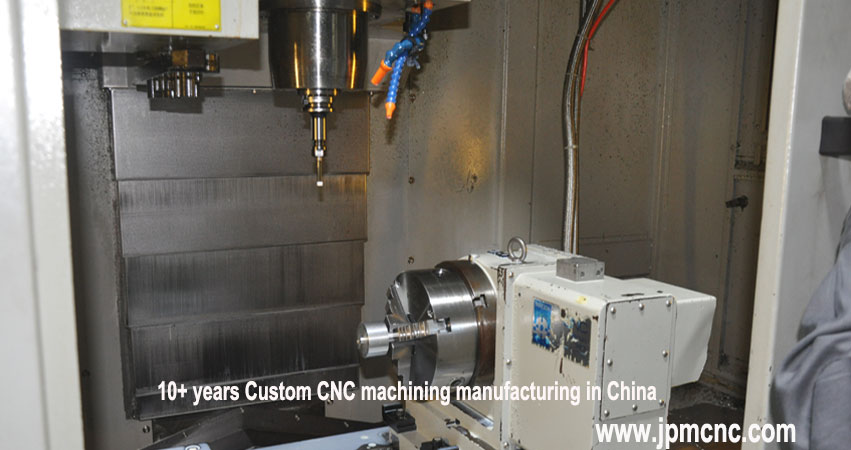
Top 8 factors of cnc precise machining and manufacturing deviationTool geometry deviation
2.Tool geometry deviation
Any tool is inevitably subject to wear during the cutting process. This causes changes in the size and shape of the parts. The influence of tool geometry deviation on machining error differs depending on the type of tool. When machining with a fixed-size tool, the manufacturing error of the tool directly affects the machining accuracy of the machined parts. While for general tools (such as turning tools, etc.), the manufacturing error There is no direct effect on machining deviation.
3.Fixture & Jigs geometry deviation
The role of the fixture is to make the machined parts correspond to the correct position of the tool and the machine. So the geometric error of the fixture has a great influence on the machining error (especially the position error).
4. The positioning deviation of precise machining and manufacturing
The positioning deviation mainly includes the base misalignment deviation and the positioning inaccurate manufacturing deviation. When machining with a machine tool, several geometric elements on the workpiece must be considered. As the positioning reference during machining, if the selected positioning reference and design reference (the reference used to determine the dimensions and position of a certain surface on the part drawing) ). If not coincident, there will be benchmark misalignment errors.
The workpiece positioning surface and the jig positioning element together constitute the positioning pair. Since the positioning pair is inaccurately. And the maximum displacement of the workpiece is caused by the matching clearance between the positioning pairs. The positioning pair called an inaccurate error. Inaccurate errors in positioning and manufacturing only produce when using the adjustment method and can not produce in the test cutting method.
5.Manufacturing Process deviation due to force-deformation
5.1 Workpiece rigidity
If the workpiece stiffness is relatively low in the processing system relative to machine tools, tools and fixtures. Under the action of cutting force, the deformation due to insufficient rigidity of the workpiece has a greater influence on the machining error.
5.2 Tool Stiffness
The external turning tool is very rigid in the normal (y) direction of the machining surface, and its deformation is negligible. The smaller diameter borehole, the poor rigidity of the knife bar, the deformation of the knife bar has a great influence on the hole processing accuracy.
5.3 Machine tool component stiffness
In Precise Machining and Manufacturing, machine tool components consist of many parts with no simple rigidity calculation method. The main method is to determine the stiffness of the machine tool component by using experimental methods. The factors affecting the rigidity of machine tool components include the influence of contact surface deformation. The influence of friction force, the influence of low-rigidity components, and the influence of clearance.
6. Machining adjustment deviation
In every process of mechanical processing, the ordinarily or every adjustment of the processing system always generate . Because adjustments cannot be absolutely accurate, adjustment errors occur. In the processing system, the mutual position accuracy of the workpiece and the tool on the machine tool is ensured by adjusting the machine tool, the tool, the fixture, or the workpiece. When the original precision of machine tools, tools, fixtures. And workpiece blanks meets the process requirements without considering dynamic factors, adjustment errors play a decisive role in machining errors.
7. Measurement deviation
When precise machining and manufacturing parts are measured during or after processing. Measurement methods, gauge accuracy, and workpiece and subjective and objective factors directly affect the measurement accuracy.
8. The internal stress of workpiece causes deviation
The stress that exists on the part without external force is called internal stress. Once the internal stress generate on the workpiece, it will cause the workpiece metal to be in an unstable state with a high energy level. It instinctively transforms to the stable state of the low energy level and accompany with deformation, so that the workpiece will lose its original machining accuracy.
if you are a designer or sourcing team, JINGXIN precision machining services in China welcome you contact us for your project. If there is anything we can do for you, just send us an email at enquiry@jpmcnc.com, we shall be more than pleased to do so.