How to operate injection molding?
- Temperature control-How to operate injection molding?
plastic-injection-molding-companies
Set the suitable temperature on the control panel, and the sensor display will be compared with the temperature generated at the set point. In this simplest system, when
the temperature reaches the set point, it will turn off and the power will turn on again after the temperature drops. This system is called open and close control, because it is not open is off.
- Temperature
Temperature measurement and control is very important in injection molding.Understanding how to operate injection molding begins with mastering temperature control.Although these measurements are simple, most of the injection molding machines do not have enough temperature probe. In most injection molding machines, the temperature is sensed by thermocouples. A thermocouple is basically composed of two different wires. If one end of the heat than the other end, then it will produce tiny telecommunications, the more the heat, the stronger the signal.
- Melt temperature
The melt temperature is very important.The melt temperature can be measured at the nozzle or measured using an air jet. The temperature setting of the feed cylinder depends on the melt temperature, the screw speed, the back pressure, the amount of charge and the injection cycle.
If you do not have the experience of processing a particular plastic, start with the lowest setting. For ease of control, the shot cylinder is divided into several zones, but not all are set to the same temperature. If the operating time is long or operating at high temperatures, set the temperature of the first zone to a lower temperature which will prevent the plastic from melting and shunting prematurely. Before the start of injection molding, please make sure that the hydraulic oil, hopper seal, mold and shot cylinder are at the correct temperature.
- Injection pressure
This is the pressure that causes the plastic flow and can be measured using a sensor on a nozzle or a hydraulic line. It does not have a fixed value, and the more difficult to fill the mold, injection pressure also increased, injection line pressure is related to injection pressure.
- The first stage pressure and the second stage pressure
During the filling phase of the injection cycle, high injection pressure may be required to maintain the injection rate at the required level. After the mold is filled, no longer need high pressure. However, in the injection of some semi-crystalline thermoplastic (such as PA and POM), due to sudden changes in pressure, will make the structure worse, so sometimes no need to use the secondary pressure.
- Mold clamping pressure
In order to counter the injection pressure, you must use the clamping pressure, do not automatically select the maximum value available, but to consider the projected area, calculate a suitable value. The projected area of the injection molded part is the maximum area seen from the application direction of the clamping force. For most injection cases, it is about 2 tons per square inch or 31 trillion Newtons per square meter. However, this is only a low value and should be a very rough experience value, because once the injection molded parts have any depth, then the side wall must be considered.
- Back pressure
This is the pressure required to produce and surpass the screw before the back pressure, although the use of high back pressure is conducive to uniform dispersion of pigment and plastic melting, but at the same time to extend the screw back to the time, reduce the length of fiber filled with plastic, and increase The pressure of the injection molding machine; so the lower the better the back pressure, in any case, can not exceed the injection molding machine injection pressure (maximum quota) of 20%.
- Injection speed
This refers to the speed of the mold when the screw is used as a punch. Injection of thin-walled products must be used high-speed, so that when the melt is not solidified when the mold is completely filled to produce a more smooth surface. Fill with a series of programmed firing rates to avoid defects such as jetting or trapping. The injection may be carried out in an open-loop or closed-loop control system.
9. Nozzle pressure
The nozzle pressure is the pressure inside the nozzle. It is about the pressure caused by plastic flow. It does not have a fixed value, but with the difficulty of filling the mold increases and increased. There is a direct relationship between the nozzle pressure, the line pressure, and the injection pressure. In the screw injection molding machine, the nozzle pressure is about 10% less than the injection pressure, and in the piston injection molding machine when the pressure loss can reach 50 percent.
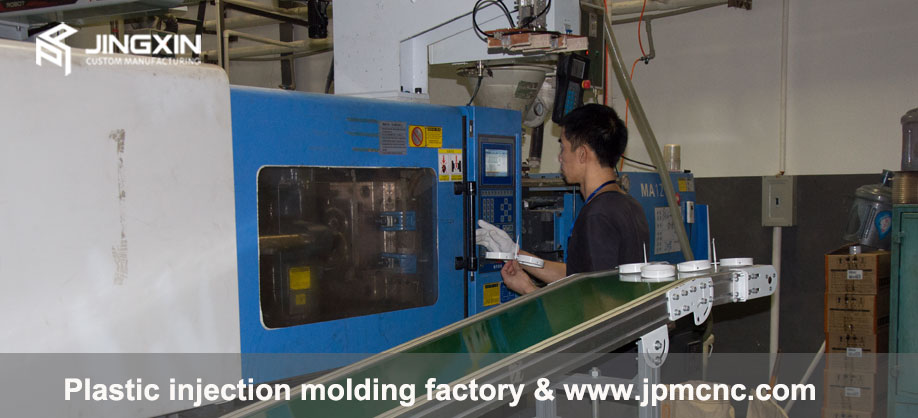
how-to-operate-injection-molding
For further information on how to operate injection molding, visit our pages on the plastic injection molding process and the case study of injection molding. If you would like to know more about JINGXIN Precision Machinery Limited, please go to our Capabilities & Services and Manufacturing or About Us pages. if you have a new project that needs plastic injection molding parts, please send us your 3D model via email at enquiry@jpmcnc.com to get an instant quote.
Related Post: